BASIC CERAMIC SHAPING METHODS 4: CASTING METHOD
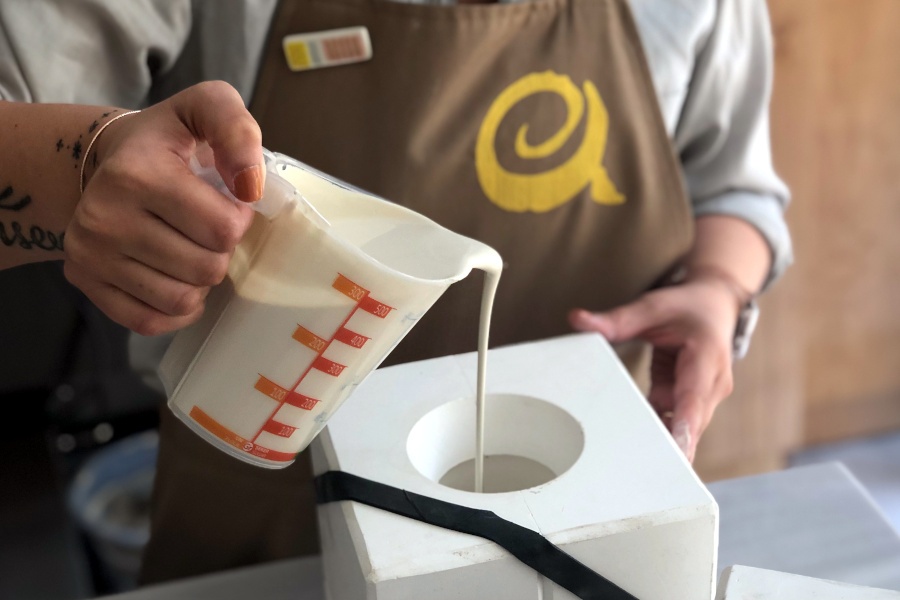
BASIC CERAMIC SHAPING METHODS 4: CASTING METHOD
The casting method is a way to shape ceramics by pouring or pumping deflocculated/liquefied, low-water-content liquid clay into plaster molds.
Casting facilitates the mass production of ceramic products, doesn't require any special machinery or equipment, and can be done in a workshop. Depending on how many molds you have, you can create hundreds of identical pieces using the casting method. It allows for easy production of parts that are difficult to create with a potter's wheel or freehand shaping. It's a very flexible shaping method, able to shape a wide range of products from delicate, precise porcelain to heavy ceramic products.
WHAT CLAYS ARE USED AS CASTING CLAY?
You can get your casting clay as a ready liquid or prepare casting clay sold in powder form according to the manufacturer's recipe. It's also possible to prepare casting clay with the right raw materials or turn the clay you use in your workshop into casting clay.
Grogs are not very suitable for the casting process. Grog will generally not stay suspended well in casting clay. It can negatively affect the flow properties of casting clay and can be abrasive on casting clay making and mixing equipment.
HOW IS CASTING DONE?
- Before casting, check if there is dry clay or dust inside the molds.
- Clean the dirt in the molds with compressed air or a soft dry brush. Never use water, you could damage the mold.
- Arrange the molds according to the casting order: heavy molds first, then medium-sized, then small molds.
- Attach the molds tightly with rubber.
- Stir the casting clay just before starting casting and check for air bubbles.
- Pour the casting clay slowly and evenly into the mold, without stopping or splashing. The casting clay should hit the bottom of the mold.
- Fill the mold every 5-10 minutes.
- Wait until the casting reaches the correct thickness.
- A good mold can be used 2 to 4 times a day, depending on air conditions. Each mold should be dried in the sun or a drying cabinet before each casting. Otherwise, molds wear out quickly.
- After reaching the correct thickness, drain the excess casting clay. If you are pouring the casting clay into the main container, strain it through a coarse sieve to catch plaster and dry clay particles.
- Then, hold the mold upside down until the clay hardens enough to be removed.
- When the clay starts to separate from the plaster mold, remove the casting product.
DOES CASTING CLAY AGE?
The prepared casting clay should be used within 2-3 weeks. Carbon dioxide in the air acts as a flocculant, making the casting clay less fluid. Aging can be slowed by keeping the casting clay in an airtight container.
HOW IS CASTING CLAY RECYCLED?
All leftover casting clay should be kept in plastic condition and in closed containers. Recycle by adding a maximum of 20% leftover clay to a new mixture. More than 20% can affect the quality of the casting clay. Be sure to consider the manufacturer's warnings on this. Always sieve the leftover clay when adding it to your casting clay to prevent dry clay or plaster particles. Great care is required to prevent contamination, especially from plaster molds.
Tutorial :
Source :
- https://www.thesprucecrafts.com/how-to-slipcast-ceramics-4154220
- https://digitalfire.com/glossary/slip+casting
- http://www.nzdl.org/cgi-bin/library?e=d-00000-00---off-0hdl--00-0----0-10-0---0---0direct-10---4-------0-1l--11-en-50---20-about---00-0-1-00-0-0-11-1-0utfZz-8-10&cl=CL3.21&d=HASHad1f112965c45034958718.8>=1
- https://walkerceramics.com.au/resources/fact-sheets/mixing-casting-powders/